
KILN INLET GAS
ANALYSIS SYSTEM
Why this Project?
As a part of a CAPEX project, I took up the challenge of enhancing the usability and experience of a Kiln Inlet Analyser.
In my career, I have always pondered on the ways in which the field instruments can be designed better so that it is can be used as more than just a measurement tool.
What is Kiln gas analysis?
Kiln inlet gas analysis systems deliver essential data. Cement plants need reliable online analysis of the process gases at the kiln inlet if they are to compete in a tough market.
​
Use the data to optimise safety, operating costs, production and emissions – and to compete with the best in the cement industry.
Why is the need?
No kiln operator would trust data from an unreliable inlet gas analysis system. The risks to safety and loss of production are too high.
​
Apart from accuracy and reliability it should also be easy to maintain, so that we can cut down on time-consuming maintenance checks.
Challenge:
How can I increase the usability of the Kiln inlet analyser beyond being just used as a measurement tool? Also, how do I ensure the equipment availability for the production professionals and ease in maintenance for the technicians by considering all safety aspects.
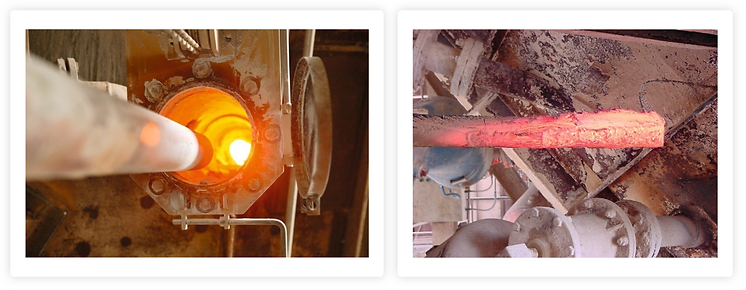
Typical Gas analyser probe looks like
Process:
As can be seen, the probe is generally exposed to high temperature. How can just a metallic probe sustain longer without any conditioning? This project helped me in thinking out of the box and beyond my usual approach as an Automation Engineer.

Empathize:
​
Let’s empathise with the users and understand the problem right from the horses mouth.
I definitely knew what it is like to carry out maintenance in the analyser and the kind of changes that I would like to make in it to suit it to my experience, but how should I solve the problems for others and who all are these users? I feel it is always better to empathise with users when you design something for them.
I started with framing questions for the user groups.
I narrowed down our 'users' to two groups.
​

After user identification, I started with the interviews
Here are my interview questions. I did iterate them as per my users responses, making it tailored to their scenario.
​
1. How often do you visit/ observe the sample readings of Kiln inlet analyser? Does it show the accurate readings as per you?
2. What is the approx. duration you spend on inspection and maintenance of Kiln inlet analyser system?
3. What chronic issues do you face during maintenance/ operation of Kiln inlet analyser?
4. How long does the sample probe last? Is it convenient to replace the sample probe? How safe is it to replace the probe in live process duct?
5. How do you rate the availability of this system? What challenges do you face when the system is not available?
​
The user responses are articulated below:
User 1
Personal details: Age-55 yrs, Work experience-32 yrs
Job: Instrumentation Technician
Bio: He is an Instrumentation shift technician who is always on the lookout for ways to break the mold and solve long standing problems. He loves to keep himself updated with the new industry updates by speaking to professionals and others in his industry to keep himself on the pulse.
Behaviour: Self driven, creative, organised
Pain Points:
1. Feels frustrated to frequently replace the sample probe in Kiln inlet analyser as his shift routine job gets effected.
2. Concerned about his safety while being exposed to live hot process duct during probe replacement.
User 2
Personal details: Age-29 yrs, Work experience-7 yrs
Job: Instrumentation Engineer
Bio: He is an Instrumentation shift Engineer. He is at tech geek who loves reading and gives his opinion on the new things happening around. His job is to manage the shift operations, technicians and rectify the issues at site to ensure smooth process operation.
Behaviour: Tenacious, Analytical skill, problem solving
Pain Points:
1. Difficult to manage technician and resources for probe shifting and replacement in night shift.
2. Unable to address and rectify other issues at site during probe burnout case.
3. Manual cleaning and maintenance is tie consuming process.
User 3
Personal details: Age-54 yrs, Work experience-30 yrs
Job: CCR operator (Production)
Bio: He has been looking after the process operations and has got a huge experience to his belt. He is very tech savvy and loves to help others. On daily basis, if there is any problem, he provides the information for rectification to the service departments and also prefers to deal with it personally. He wants the system to be easy and intuitive.
Behaviour: Versatile, flexible and focused
Pain Points:
1. Unable to optimise fuel consumption and reduce emission.
2. No control on kiln pyro during breakdown of analyser, resulting in poor clinker quality.
User 4
Personal details: Age-45 yrs, Work experience-21 yrs
Job: Section Head (Production)
Bio: He is responsible to ensure optimised and smooth process operation and also keep stakeholders/ service departments informed about the process changes and its impact. His reports have an impact on the senior managements decision making, so he is highly focused.
Behaviour: Leadership /analytical skills
Pain Points:
1. Downtime costs big time. Once CO or SO2 builds up Kiln has to be stopped at least for 3 hrs.
2. No pyro control can lead to disastrous consequences on safety of working environment.
3. KPI's get a poor impact with production loss. All his efforts goes in vain on such cases.
With each interview, my questions started becoming better and I felt the need to ask more. After finishing the interviews and documenting the inferences, I also felt like I wanted to ask some extra questions.I did manage to ask some of these during the Site visit with users, while for others, I made observations from the site visit experience shared by my users.
​
Define:
​
On the basis of the data collected, I made the following inferences on the key problems faced by my users:



Ideate:
​
What is the need of the hour? Which problems stand out? Why is it important to address them? This is the stage where I entered into an extensive brainstorming session, actually bifurcating the problem areas and nudging for the solution which might solve some or all of them.
Here is the initial list of ideas that resulted from the brainstorming session :
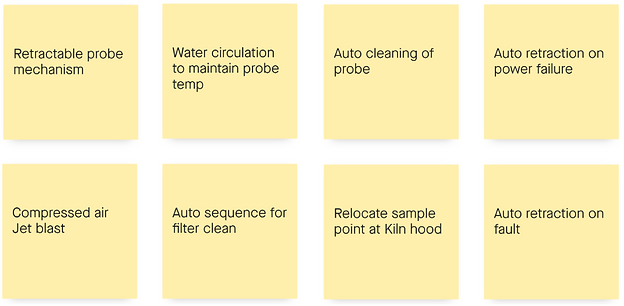

After whacking my brains a little more, I shortlisted the following three solutions.
1. Retractable probe with water circulation mechanism to maintain probe temperature and ensure frequent burnout.
2. Relocation of sampling point to eradicate the impact of false air in the system.
3. Auto cleaning mechanism to increase the equipment availability.

Prototype:
​
On prioritizing the above task , I observed that all the remaining pain points too can be addressed as the byproduct of these ideas. Like reduced manual intervention, fuel optimization, avoid production loss, reduced maintenance etc.
I decided to go through with prototype 1 since it was promising and addressed most of the pain points of my users.

Test:
​
The prototype was presented to the 8 concerned users to get their feedback in initial stage. We arranged a 2hr feedback session at conference hall where I presented the prototype and the feedback was given.
The users really liked the presentation and the prototype. They said that it solved most of their issues and that they would love to get one installed at site with new sample point. Meanwhile it was also decided to keep the existing one in line to observe and derive the benefits from this design model.
Implement:
​
We then proceeded with the CAPEX approval process and commissioned and implemented the approved design at site in just 8 months (Target duration of project completion- 10 months)

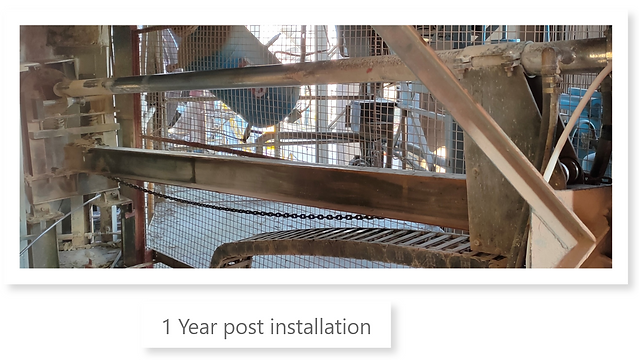
Achievements and feedback:
After one year of installation, I again had a feedback session with same set of users to know about further issues if they are still facing, as expected all users were satisfied with the performance of newly installed analyser system. They now wish to have the system installed for line 1 and 2.
Major achievements include:


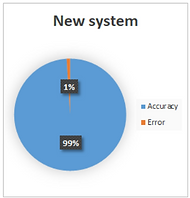
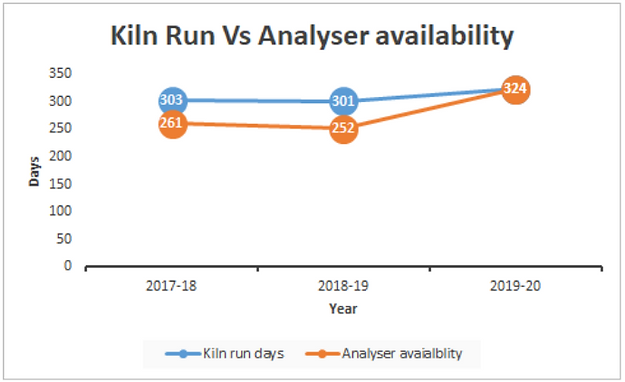
My Learnings:
The project was very intense. I went through a series of emotions while conducting the exercise. It started with excitement to do something new, followed by being clueless on where to start and how to move on. I was tempted to search for solutions provided by other product designers across the world. I was also tempted to take the easy route and propose something ordinary. Somewhere in between the project I decided to think outside the box and propose something that would actually excite my users.