
CEMENT BAG
DIVERTER
Why this Project?
I took up the challenge of enhancing the usability and experience of workmen at bag diverters in packing plant, as a part of a improvement project.
​
I have always pondered on the ways in which the field equipment's can be designed better so that it is can enhance the usability & experience of the one using it.
What is a Bag diverter?
Bag diverter is used for diverting the cement bags from the running belt conveyors.
There are basically two types of cement bag diverters:
1. Powerless bag diverters- wheel type.
2. Motorised belt type bag diverter.
Why is the need?
There were many issues associated with it like idle running of diverters, absence of engaged manpower at the time of need at site and many more.
Contract workmen engaged in this work were also concerned about there safety and health issues.
Challenge:
​
How can I enhance the experience of workmen at cement bag diverter beyond being just called loaders/ diverters at site? What exactly is the issues they are facing?Also, how do I ensure the equipment availability for the operation professionals and ease in handling the equipment by considering all safety aspects.

Process:
​
As can be seen, the bag diverter is mounted on a belt conveyor. How pathetic it could be to repeatedly pull and divert it to the desired direction in a manual process . This project helped me in thinking out of the box and beyond my usual approach as an Automation Engineer.

Empathize:
​
Let’s empathise with the users and understand the problem right from their site experience.
I definitely knew what is a cement bag diverter and why is it being installed at site but to make any kind of changes that would suit the users experience, it is better to know how should I solve their problems and who all are the ones using it? I feel it is always better to empathise with users when you design something for them.
I started with framing questions for the user groups.
I narrowed down our 'users' to two groups.

After group formation for users, I started with the interviews
Here are my interview questions. I did iterate them as per my users responses, making it tailored to their scenario.
1. How often do you need to use the diverter for shifting of bags? Elaborate your experience.
2. What is the approx. duration you spend on diverting the bag diverter? What do you do in the time gap between switching of two bag diverters?
3. What chronic issues do you face during cement bag diverter operation?
4. How safe is it to switch the diverters manually on a running belt conveyor?
5. What issues do you face in operational point of view?
​
The user responses are articulated below:
User 1
Personal details: Age-45 yrs, Work- Contract workman
Job: Diverter attendant
Bio: He has primary education. He works on contract basis. His job is to divert cement bags on belt conveyor using manual belt diverters and in few occasions load bags on truck. He comes from a nearby village and earns his bread and butter by working here. He is well aware of all safety standards.
Behaviour: Altruistic, Anxious
Pain Points:
1. Feels frustrated to change the diverters manually in such hot & dusty atmosphere and to clear bag jamming.
2. Concerned about his safety while diverting a bag diverter on a running belt .
User 2
Personal details: Age-39 yrs, Work Experience- 15yrs
Job: Senior Operation Engineer
Bio: He has done his graduation in Mechanical Engineering. He looks after the smooth operation of Cement Packing Plant. He is very tech savvy and loves to help others. He always inspires his contract workmen to get the best out of them.
Behaviour: Compassionate, curious, logical
Pain Points:
1. Frequent bag jamming at diverter end delays rack loading & increases the demurrage charge on racks.
2. At few occasions, due to not availability of workmen at site for bag diversion, operation gets delayed.
3. Increased truck turn around time is also a concern.
User 3
Personal details: Age-54 yrs, Work experience-30 yrs
Job: CCR operator (Packing Plant)
Bio: He has been looking after the process operations in packing plant and has got a huge experience. On daily basis, if there is any problem, he provides the information for rectification to the operation and maintenance concerned. He wants the system to be simple and easy rather than making it complicated
Behaviour: Organised and precise
Pain Points:
1. Unable to know the actual status of bag diversion, confirmation of status from workmen is time consuming.
2. Excessive manual intervention in the process leads to delay and powerloss.
User 4
Personal details: Age-41 yrs, Work experience-17 yrs
Job: Section Head (Packing plant)
Bio: He is responsible to ensure optimised and smooth loading of cement and clinker and also keep stakeholders/ service departments informed about the operational changes and its impact. His reports have an impact on the senior managements decision making, so he is highly focused to achieve all the targets.
Behaviour: Leadership /analytical skills, Persuasive
Pain Points:
1. Downtime costs big time. Increased demurrage on racks is a concern.
2. Increased man power and manual intervention imposes high risk factor at site on terms of safety.
With each interview, my questions started becoming better and I felt the need to ask more. After finishing the interviews and documenting the inferences, I also felt like I wanted to ask some extra questions.I did manage to ask some of these during the Site visit with users, while for others, I made observations from the site visit experience shared by my users.
​
Define:
​
On the basis of the data collected, I made the following inferences on the key problems faced by my users:


Segregating the problem statements under different sections helped me in prioritising the issues and thus narrowing down my ideas to those particular solutions.
​
Ideate:
​
What is the need of the hour? Which problems stand out? Why is it important to address them? This is the stage where I entered into an extensive brainstorming session, actually bifurcating the problem areas and nudging for the solution which might solve some or all of them.
Here is the initial list of ideas that resulted from the brainstorming session :


On prioritizing the above task , I observed that all the remaining pain points too can be addressed as the byproduct of these ideas. Like reduced manual intervention, power optimisation, risk factor with manpower at site etc.

Prototype:
​
I decided to go through with prototype 1 since it was promising and addressed most of the pain points of my users.


Test:
​
The prototype was presented to the 13 concerned users to get their feedback in initial stage. We arranged a small feedback session at site where I presented the prototype and the feedback was given.
The users really liked the prototype. They said that it solved most of their issues and that they would love to get one installed at all diverter points. Meanwhile it was also decided to carry out the modifications in the existing one on a phased manner/ opportunity basis to avoid demurrage and delay in operation.
​
Implement:
​
We then proceeded with the approval process and commissioned and implemented the approved design at site in just 5 months (Target duration of project completion- 8 months).


Achievements and feedback:
Major achievements after first 6 months of all installation include:
1. With automation of bag diverter, we removed all the 12 contract workman at site engaged in bag diversion and were shifted them to other tasks thereby reducing the risk factor on safety.
2. After interlocking bag diverters with belt conveyors, we could avoid idle running of diverters and reduce /optimise the power consumption.
3. With installation of proximity sensors on diverters, status of diversion could be visible at control room and the unwanted delay was eradicated.
4. Truck turn around time reduced to 2 hrs from earlier 5 hrs.
5. There was no demurrage on rack resulting from bag jamming/ diversion issues.
6. Reduced power consumption & manpower helped to save INR 21 lacs annually.
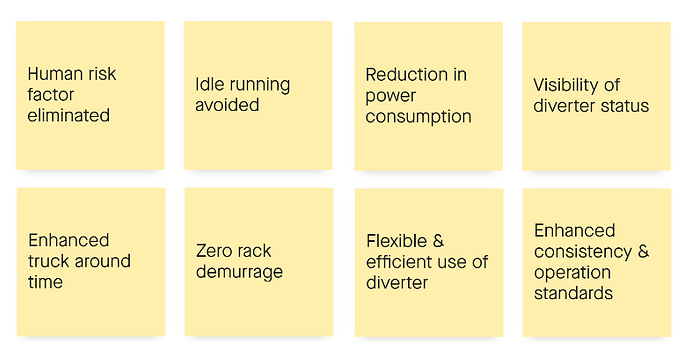




My Learnings:
The project was very challenging. I went through a series of reactions while conducting the implementation. It started with excitement to do something new, followed by being clueless on where to start and how to move on. I was curious to search for solutions based on user problems. Sometimes I also felt how language barrier can also be a factor in user interviews.